Tips
What is Direct Expenses? Understanding Their Role in Business
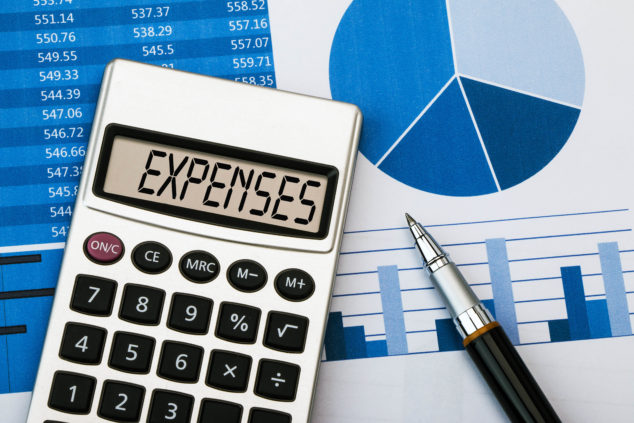
Understanding direct expenses is crucial for managing your business’s financial health. Direct expenses refer to costs that are directly tied to the production of goods or services your company provides. This category of expenses includes materials, labor, and any other costs that fluctuate with your production levels.
Recognizing and accurately categorizing these expenses can help you gain insights into your profitability. By tracking direct expenses closely, you can make informed decisions about pricing, budgeting, and resource allocation. This knowledge empowers you to fine-tune your operations and improve your bottom line.
As you explore this topic further, you’ll discover examples and detailed explanations that will clarify how direct expenses affect your financial reporting. Understanding these costs not only aids in compliance with accounting standards but also enhances your strategic planning.
What is Direct Expenses?
Direct expenses refer to costs that you can directly link to the production of goods or services. They are typically variable costs, which means they fluctuate with the level of production.
For instance, materials used in manufacturing are direct expenses because they’re essential for creating the final product. Labor costs associated with producing that product are also direct expenses.
Characteristics of direct expenses include:
- Traceability: You can trace these costs directly to a cost object.
- Variability: Often, these expenses vary based on production levels.
- Fixed Elements: Some fixed costs, such as rent for a dedicated facility, can also be considered direct if they are specifically tied to production.
Examples of Direct Expenses
Identifying direct expenses helps you evaluate project costs more effectively. Here are examples commonly seen in various industries:
- Raw Materials: The cost of materials used in production, like steel for manufacturing cars.
- Direct Labor: Wages paid to workers who are directly involved in production activities.
- Manufacturing Supplies: Items consumed in the production process, such as lubricants or cleaning materials.
In a consulting firm, direct expenses might include travel costs incurred for a specific client project. By monitoring these costs, you can better understand the profitability of each project and make informed financial decisions.
Classification of Direct Expenses
Understanding the classification of direct expenses is essential for accurate financial management. You can break down direct expenses into three main categories: direct materials, direct labor, and direct overheads. Each plays a crucial role in the overall cost structure of your business.
Direct Materials
Direct materials are the raw materials used in the production of goods. These items can be directly traced to the finished product, making them a clear component of direct expenses. For example, if you manufacture furniture, the wood and fabric you use are direct materials.
Key Points:
- They are essential for product creation.
- The cost can vary based on market prices and quality.
- Keeping track of these costs helps in budgeting and cost control.
You should maintain accurate records of all purchases and usage of direct materials to ensure proper accounting. Doing so will help you analyze costs and make informed decisions about suppliers and pricing.
Direct Labor
Direct labor refers to wages and salaries for employees who are directly involved in the production process. This includes workers assembling products or providing services that contribute directly to the output.
Key Points:
- Direct labor costs are variable and can fluctuate with production levels.
- Benefits and overtime pay also count as part of direct labor costs.
Monitoring direct labor expenses is vital for calculating the overall production costs. By assessing labor efficiency and productivity, you can optimize workforce management and potentially lower costs.
Direct Overheads
Direct overheads consist of costs that are directly tied to the production but cannot be attributed to specific products or services. This may include expenses like machinery maintenance that are essential for operations.
Key Points:
- These costs can include utilities, rent for production facilities, and equipment depreciation.
- They often remain fixed within a certain production range.
You must identify and allocate these costs correctly to understand the true cost of production. Proper classification ensures more accurate pricing strategies and better financial planning for your business.
How to Record Direct Expenses
Recording direct expenses is essential for accurate financial management and reporting. Understanding how to account for these expenses and their impact on financial statements helps you make informed business decisions.
Accounting Treatment
When recording direct expenses, you categorize them based on their nature. Common direct expenses include raw materials, labor costs, and manufacturing supplies. You can record these costs through different methods:
- Job-order costing: Track expenses by individual jobs or projects.
- Process costing: Allocate costs evenly across all units produced.
Each method provides insights into where your money goes. It’s crucial to maintain accurate records to ensure that direct expenses are reflected correctly in your financial statements. Failure to do so may lead to skewed profitability analysis.
Impact on Financial Statements
Direct expenses directly affect your income statement and ultimately your gross profit. By tracking these costs, you can determine the relationship between production and expenditure.
When you record direct expenses accurately, your Cost of Goods Sold (COGS) reflects true production costs. This transparency allows you to analyze profitability effectively. An increase in direct expenses can reduce overall profit margins, so monitoring these costs is vital for maintaining financial health.
Therefore, regular review of direct expenses against production levels aids in strategic planning and helps identify trends that could impact your bottom line.
Management of Direct Expenses
Effectively managing direct expenses is crucial for maintaining profitability and ensuring operational efficiency. This involves careful budgeting and implementing measures to control costs.
Budgeting and Forecasting
Creating a detailed budget for direct expenses helps you plan for future costs and aligns your spending with business goals. You should categorize expenses, such as materials, labor, and utilities, to gain better insight.
- Historical Data: Review past expenditures to inform future budgets. This helps identify patterns and recurring costs.
- Monthly Projections: Estimate monthly expenses based on anticipated production levels. Adjust these projections as needed for seasonal variations in demand.
- Flexibility: Your budget should allow for adjustments in response to market changes or unforeseen costs. This adaptability can prevent overspending.
Regular budget reviews ensure you remain on track. You can make informed decisions based on analysis and historical trends.
Cost Control Measures
Implementing effective cost control measures is essential for managing direct expenses. This process helps minimize waste and optimize resource allocation.
- Tracking Systems: Utilize software or spreadsheets to monitor spending in real-time. Regular tracking allows you to spot discrepancies early.
- Supplier Negotiation: Foster relationships with suppliers. You can negotiate better terms or bulk purchase discounts to lower costs.
- Employee Training: Train your workforce on cost-saving practices. Educated employees can help identify inefficiencies and suggest improvements.
Incorporating these measures into your business strategy ensures that you keep direct expenses in check, supporting overall financial health.
Direct Expenses in Different Industries
Direct expenses vary significantly across industries, reflecting the specific requirements and operational structures of each sector. Understanding these nuances is essential for effective financial management and cost control.
Manufacturing Sector
In the manufacturing sector, direct expenses primarily consist of materials and labor directly linked to production. Key components include:
- Raw Materials: The cost of ingredients or components needed to create the finished product, such as metals, plastics, or chemicals.
- Direct Labor: Wages paid to workers who are directly involved in manufacturing. This includes assembly line workers, machine operators, and quality control staff.
Manufacturers track these costs closely since they directly impact the cost of goods sold (COGS). Effective management ensures the production process remains cost-efficient.
Service Sector
The service sector incurs direct expenses mainly through labor and other operational costs that directly contribute to providing services. Typical direct expenses include:
- Salaries: Payments made to professionals delivering the service, such as consultants, healthcare providers, and technical support personnel.
- Freelancer Costs: Payments to independent contractors or part-time staff engaged for specific projects.
Businesses in this sector often face challenges in accurately allocating these expenses, as the nature of services can be less tangible than products, affecting how costs are tracked and managed.
Retail and Wholesale
In retail and wholesale, direct expenses include the costs associated with acquiring inventory and selling products. Important aspects include:
- Inventory Purchases: Costs incurred when buying products for resale, which are crucial for maintaining stock levels.
- Sales Commissions: Payments made to sales staff or agents based on the volume of sales they generate.
Retailers must manage these direct expenses effectively to maintain profitability. Tracking the cost of goods sold accurately helps in setting appropriate pricing strategies and optimizing inventory levels.
Legal and Tax Implications of Direct Expenses
Understanding the legal and tax implications of direct expenses is crucial for effective financial management. This section covers how you can benefit from tax deductibility and ensure regulatory compliance.
Tax Deductibility
Direct expenses are often tax-deductible, which can reduce your taxable income. This includes costs directly tied to producing goods or services, such as raw materials, labor, and manufacturing overhead.
To maximize deductions, maintain detailed records. Here are some common direct expenses you can deduct:
- Material Costs: Costs of raw materials needed for production.
- Labor Costs: Wages paid to employees directly involved in the production process.
- Manufacturing Overhead: Utilities and rent for facilities involved in production.
Consult with a tax professional to ensure you correctly categorize these expenses and adhere to local regulations. This can help you avoid penalties and ensure accurate tax filing.
Regulatory Compliance
Compliance with regulations related to direct expenses is vital for your business. Tax authorities may require clear evidence of expense categorization and documentation.
You should familiarize yourself with the following regulations:
- IRS Guidelines: The IRS has specific rules on classifying direct and indirect costs. Misclassification can lead to audits or penalties.
- Industry Standards: Different industries may have additional guidelines that affect how expenses are categorized.
By ensuring compliance, you not only safeguard your business from legal issues but also enhance your credibility with stakeholders. Regularly review your expense records and keep abreast of any changes in regulations that might affect your deductions.
Direct Expenses vs. Indirect Expenses
Understanding the distinction between direct and indirect expenses is crucial for effective financial management. This knowledge will help you allocate costs appropriately and enhance your budgeting strategies.
Key Differences
Direct expenses are costs that can be directly traced to a specific product or service. For example, raw materials and direct labor fall into this category. In contrast, indirect expenses support the entire operation but can’t be tied to a single product. Common examples include rent, utilities, and administrative salaries.
Direct Expenses | Indirect Expenses |
---|---|
Directly related to production | Not directly tied to a specific product |
Easily traceable costs | Difficult to allocate to specific items |
Examples: Raw materials, wages for production | Examples: Rent, utilities, and office supplies |
Allocating Costs Effectively
Effective allocation of costs helps in creating accurate financial reports. For direct expenses, you can match costs to specific projects easily, making budgeting straightforward. For indirect expenses, you may use allocation bases, such as square footage for rent or total direct labor hours for utilities.
Ensure that your method for allocating indirect costs is consistent. This allows for comparability over time and helps in understanding true profitability across products. Consistent tracking aids in strategic planning and can improve your financial outcomes.
Challenges in Allocating Direct Expenses
Allocating direct expenses presents several challenges that can impact the accuracy of financial reporting and decision-making. Key issues include the complexity of tracking costs and ensuring the precise allocation of expenses to specific projects or products.
Complex Cost Tracking
Tracking direct expenses can become intricate, especially in environments with multiple products or services. You may find it challenging to trace costs back to specific cost objects due to shared resources.
Consider the following aspects:
- Shared Resources: Often, materials or labor contributions overlap, complicating direct allocation.
- Variability: Direct expenses may fluctuate significantly based on production levels.
- Data Sources: Gathering data from various departments or systems can introduce discrepancies.
Implementing a systematic approach to tracking is crucial for maintaining accuracy in your financial statements.
Accurate Expense Allocation
Ensuring accurate allocation of direct expenses requires methodical processes. Inconsistencies can arise, leading to misrepresentation of profitability.
Here are some critical factors to consider:
- Allocation Methods: Various methods such as job order costing may be suitable, but they come with their own sets of challenges.
- Industry Differences: Different industries may require unique approaches based on their operational structures.
- Compliance Standards: Adhering to accounting principles like GAAP or IFRS is essential for credibility.
You must establish a consistent methodology and regularly review your allocation processes to minimize errors and improve financial insights.
Emerging Trends in Expense Management
Expense management is evolving rapidly, driven by both technological advancements and strategic business decisions. Understanding these trends can help you navigate the complexities of modern finance management effectively.
Technological Advancements
Technological innovation is transforming how businesses manage their expenses. Automation tools are becoming prevalent, streamlining processes such as expense reporting, approval workflows, and real-time tracking.
Key technologies include:
- Artificial Intelligence (AI): Enhances data analysis and identifies spending patterns.
- Mobile Applications: Allow employees to submit expenses on-the-go, improving efficiency.
- Cloud Solutions: Offer secure data storage and accessibility, making it easier to collaborate across teams.
These tools not only reduce administrative burden but also enhance accuracy in financial reporting, giving you real-time insights into spending. Implementing these technologies can lead to more informed financial decisions and improved accountability within your organization.
Strategic Business Decisions
As expense management evolves, organizations are integrating it into broader strategic frameworks. You can leverage real-time data analytics to influence budgeting practices and optimize resource allocation.
Trends include:
- Cross-Department Collaboration: Encouraging different teams to share insights on expenses drives accountability.
- Sustainability Focus: More companies are factoring sustainability into their expense decisions, considering the environmental impact of their spending.
- Expense Forecasting: Businesses are investing in tools that predict future expenses based on historical data, allowing for better cash flow management.
These strategic choices not only enhance efficiency but also align your financial goals with the overall mission of your organization.
Frequently Asked Questions
How are direct expenses categorized in accounting?
Direct expenses are categorized as costs specifically tied to the production of goods or services. In accounting, they typically appear on the debit side of the trading account, reflecting their direct association with revenue-generating activities.
Can you provide some examples of direct expenses in a business setting?
Examples of direct expenses include costs like raw materials, direct labor costs, and manufacturing supplies. For instance, if you operate a bakery, the costs for flour, sugar, and the salaries of bakers directly involved in production would be classified as direct expenses.
What distinguishes direct expenses from indirect expenses?
Direct expenses are directly attributable to a specific product or service, while indirect expenses, also known as overheads, cannot be traced to a single cost unit. Indirect expenses include costs like utilities or rent, which support multiple business functions but do not directly link to production.
Are employee salaries considered direct expenses?
Employee salaries can be direct expenses if the employees perform work directly related to producing goods or services. For example, the wages of assembly line workers are direct expenses, while the salaries of administrative staff are indirect because they support the overall business operations.
In what ways do direct and indirect costs impact financial statements?
Direct costs typically appear on the income statement to calculate the gross profit, directly affecting profitability. Indirect costs are recorded as operating expenses and influence the net profit, highlighting operational efficiency and overall financial health.
How can one differentiate between direct and indirect expenses with practical examples?
To differentiate, consider the relation of an expense to production. For instance, in a construction company, the cost of building materials is a direct expense, while the cost of office supplies used for general administration is an indirect expense. This distinction helps in budgeting and financial analysis.