Uncategorized
Industrial Coding and Marking: Precision Identification for Production and Compliance
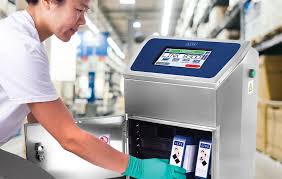
Every product that rolls off a manufacturing line—whether it’s a soda can, medical syringe, engine part, or packaged snack—needs to be identified, traced, and often legally labeled. That’s where industrial coding and marking come in. These systems provide the critical labeling information required for compliance, logistics, inventory tracking, and customer transparency.
From batch codes and barcodes to expiration dates and logos, coding and marking solutions are a vital part of modern manufacturing and packaging. In this article, we explore how these systems work, the technologies behind them, and how businesses can choose the best solution for their operational needs.
What Is Industrial Coding and Marking?
Industrial coding and marking refer to the process of applying identification information to a product, part, or package during manufacturing or packaging. These codes can be as simple as a printed best-before date or as complex as a serialized 2D barcode with full traceability back to its production batch.
Typically, this information is printed or engraved onto surfaces like cardboard, plastic, glass, metal, or film using automated machines. The process must be accurate, fast, and compatible with the production line speed and materials being used.
Common Applications of Coding and Marking
These systems are used across nearly every industry to fulfill legal, operational, and branding requirements. Common use cases include:
- Food and Beverage: Expiration dates, lot numbers, production times, and traceability data for recalls or quality assurance.
- Pharmaceuticals: Serialized barcodes, dosage information, and tamper-evident markings for regulatory compliance.
- Automotive and Aerospace: Part numbers, supplier codes, and durable marks that can withstand heat, oil, and abrasion.
- Consumer Goods: Branding elements, batch tracking, and product authenticity codes.
- Electronics: Component IDs, ESD warning labels, and manufacturing data for assembly and service.
Types of Coding and Marking Technologies
There’s no one-size-fits-all approach. The ideal technology depends on the substrate, production environment, and data required. Here are the most commonly used methods:
- Inkjet Printing (CIJ and TIJ): Continuous Inkjet (CIJ) and Thermal Inkjet (TIJ) printers are popular for their speed and ability to print on curved or uneven surfaces. CIJ is often used for high-speed bottling or canning lines, while TIJ is better suited for high-resolution printing on cartons or labels.
- Laser Marking: Uses high-energy light to etch or engrave a mark onto the product surface. Offers permanent, high-contrast marks without consumables, making it ideal for electronics, metal parts, and medical devices.
- Thermal Transfer Overprinting (TTO): Transfers ink from a ribbon onto film or flexible packaging using heat and pressure. Provides crisp, consistent codes for labels and flexible pouches.
- Dot Peen Marking: Uses a stylus to indent characters or codes into hard materials. Known for durability in harsh environments, especially in metal and automotive industries.
- Print-and-Apply Labeling: Applies pre-printed or real-time labels with variable data directly to products or cases. Useful for shipping, logistics, and retail compliance.
Benefits of Modern Coding and Marking Systems
Upgrading to an advanced coding and marking system brings multiple benefits to your production line and bottom line:
- Compliance: Meet global and industry-specific regulations for traceability, safety, and product labeling.
- Improved Traceability: Enables complete tracking of products from manufacture to delivery, aiding in recall management and quality control.
- Higher Production Efficiency: Automated systems run at high speeds and integrate with production lines without slowing output.
- Reduced Waste: Consistent, accurate codes minimize misprints and product rejections.
- Enhanced Brand Protection: Secure codes and serialization help prevent counterfeiting and ensure authenticity.
Choosing the Right Coding and Marking Solution
To select the best technology for your operation, consider the following:
1. Substrate Type: Not all printing methods work on all materials. For example, laser systems are excellent for metals, while inkjet is better for plastics and films.
2. Line Speed and Volume: High-speed production lines require printers that can keep up without sacrificing quality or resolution.
3. Data Requirements: Determine if you need static codes, real-time date stamps, variable data, or serialized barcodes.
4. Environment: Harsh conditions—such as dust, moisture, or temperature extremes—require rugged equipment and specialized inks or engraving methods.
5. Integration and Maintenance: Look for systems that integrate easily into your existing workflow and offer simple maintenance with minimal downtime.
Marking the Future of Manufacturing
Industrial coding and marking systems are no longer just compliance tools—they’re strategic assets. They improve traceability, safeguard brand reputation, and enable smarter inventory and logistics management. As automation and digital supply chains evolve, these systems are becoming more intelligent, with built-in diagnostics, remote monitoring, and smart data capabilities.
Whether you’re a small-scale producer or a global manufacturer, investing in the right coding and marking solution can significantly elevate your operational accuracy and efficiency. With so many technologies available, partnering with an experienced integrator or supplier is key to customizing a solution that fits your industry, budget, and future growth goals.